8 of the best men’s shoes for summer from HEYDUDE
Jul 4, 2025Part 2 (lapels) – Permanent Style
- Sep 2, 2024
- 0 Comments
133
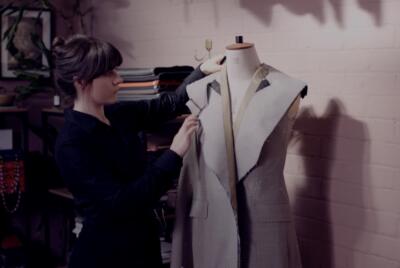
In this, the second of our films looking at the details of making a bespoke suit, we’re focusing on lapels.
But not necessarily the hand padding – that most obvious sign of handwork, which you can see on the back of most bespoke lapels. We’ve covered that before and a lot of readers are familiar with it.
Frankly, it’s also the kind of thing people can focus on at the expense of the more important things – like what you’re actually doing with that stitching. How much are you shaping the chest and why? What other layers and pieces are going on there?
In this video, you’ll see the tailor Jennie Adamson begin with an aspect of bespoke we’ve never even mentioned – using a strip of lining to control the break line (where the lapel folds over).
This is done with the lining on the straight, running counter to the bias (diagonal) of the main cloth. This is to help stop it stretching – and Jennie also draws in the material, tightening it with her thread before shrinking away that fullness with the iron. You can see more about how shrinking works in this previous video.
I hope you enjoy it and, as with the first video on pockets, it gives you some newfound appreciation of your bespoke garment. They really are marvels.
Jennie is a a coatmaker for Gieves & Hawkes, a pattern maker for brands like The Deck and Casablanca, and a cutter and maker of her own tailoring. More on her here. The location is Cockpit Arts in Bloomsbury, a wonderful home for craftspeople that’s just behind Lamb’s Conduit Street.
Thank you to Vitale Barberis Canonico for supporting this series. The cloth we used is my favourite VBC material, the four-ply high-twist wool in the Ascot bunch from Drapers. The suit being made is for Jennie, and I am wearing my suit from Assisi in the same material.
You can see the first video in the series here. Other similar videos are:
Publisher: Source link