8 of the best men’s shoes for summer from HEYDUDE
Jul 4, 2025News
A revolutionary electronic skin fabrication process brings us closer to a sixth ‘magnetic perception’ sense
- Aug 14, 2024
- 0 Comments
231
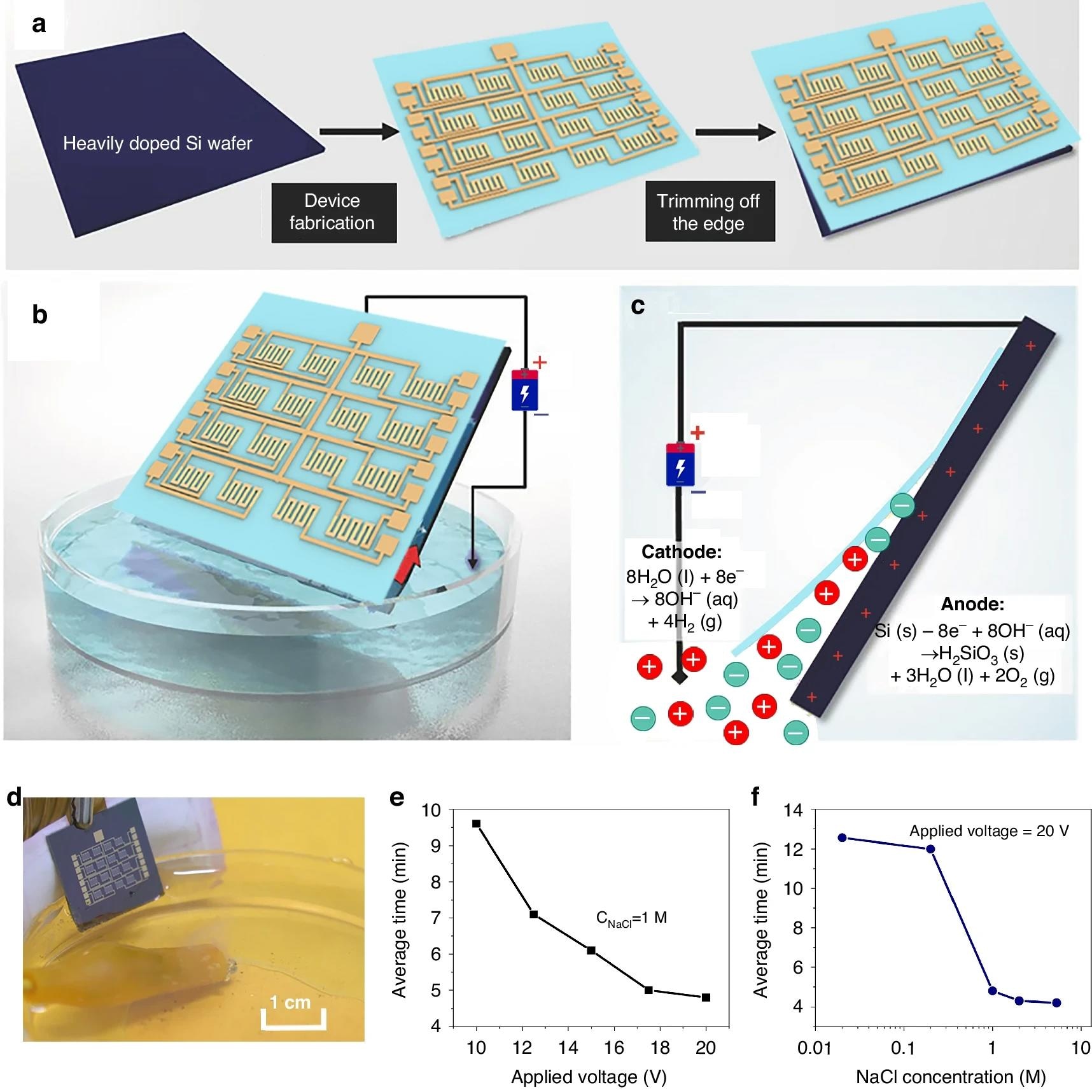
In a recent study published in the journal Microsystems & Nanoengineering, researchers describe a groundbreaking novel fabrication process for a touchless interactive device (‘skin’) using a flexible giant magnetoresistive (GMR) sensor array. Current-generation flexible magnetoelectronic skins suffer from three fundamental shortcomings: low sensitivity, non-destructive delamination (fabrication) challenges, and minor magnetic field detection difficulties.
The current work addresses these shortcomings by presenting a novel electrochemical delamination process that produces an ultra-thin, multilayer GMR system that maintains performance even after repeated bending (up to 90 degrees). Test devices using this fabrication process demonstrated significant improvements over conventional systems in durability (especially bending-associated), pressure sensing, and non-contact interaction. This work represents the first step towards a new generation of high-performance flexible magnetic sensors, paving the way for more sophisticated wearable skin technologies.
Background
The past two decades have witnessed unprecedented surges in the usage and applications of electronic wearables, particularly in the sphere of human-to-machine interfaces (HMIs). One such application, ‘electronic skins,’ aims to replicate natural skin functionality with added health monitoring and movement tracking capabilities. Current research seeks to augment this functionality by enabling the development of ‘magnetic perception,’ a novel ‘sixth sense.’ This functionality is achieved using giant magnetoresistive (GMR) sensors composed of tunneling magnetoresistive (TMR), giant magnetoimpedance (GMI), anisotropic magnetoresistive (AMR), or Hall sensors. Unfortunately, conventional fabrication processes involving depositing Co/Cu, Py/Cu, or Pd/Co stacks onto ultrathin foils present multiple shortcomings. Notably, the fabrication process is often manual and inefficient, preventing standardized mass production. Furthermore, devices based on the finished product demonstrate low sensitivity to weak magnetic fields and low durability.About the study
The present study aims to overcome these challenges by demonstrating the fabrication and performance of a novel electrochemical delamination process that allows for the non-destructive detachment of ultrathin films from their rigid substrate. This process not only enhances efficiency but also minimizes damage, resulting in a GMR spin valve structure with high magnetic sensitivity, a bending angle of 90°, and no observable performance degradation even after repeat bending.Fabrication
Fabrication of the novel GMR sensor is achieved using a multistep electrochemical delamination procedure. First, a substrate comprised of a heavily doped silicon (Si) wafer (resistivity = 0.002 to 0.004 Ω cm) with a superimposed thin polymer layer is developed. Secondly, conventional microfabrication processes are used to fabricate GMR devices on the polymer layer. Thirdly, the construct is introduced into a sodium chloride (NaCl) electrolyte aqueous solution, and the edges of the polymer layer are trimmed to allow direct contact between the Si wafer and the NaCl solution. Finally, applying a positive and negative potential to the NaCl solution triggers an anodic reaction, resulting in the formation of oxygen (O2) bubbles that, in turn, facilitate the separation of the Si and polymer layers. Notably, this process can be automated and is devoid of mechanical and chemical damage characteristic of conventional GMR manufacturing approaches.“This method demonstrates superiority over other delamination techniques due to its distinctly straightforward, notably rapid, noninvasive, and adaptable nature.”The free-standing polymer film thus obtained can easily be laminated onto target surfaces for the creation of GMR multilayer structures and the subsequent development of HMIs.
Performance
A magnetic resonance (MR) sensor testing platform was used for pilot device performance testing. GMR ratios were observed to reach 5.6%, matching conventional antiferromagnetic layer-based GMR devices. Following delamination, GMR ratios decreased to 2.46%. However, low magnetic field sensitivity significantly outperformed previous methodologies (10 Oe before and 80 Oe following delamination versus 4 kOe). The surface roughness of the spin-coated polyimide was assessed using atomic force microscopy (AFM) and was revealed to be 0.574 nm. Comparisons of device curves before and after delamination were observed to be near-identical, confirming that the present delamination process had a close-to-no impact on final GMR performance. Bending performance was evaluated using a custom-designed flexible circuit board. The GMR ratio was observed to remain at 2.46% across bending angles from 0° to 90° with resistance fluctuating by less than 6 Ω (initial resistance = 1600 Ω), further underscoring the device’s durability.“These attributes collectively indicated that the GMR system could be affixed to any part of the human body and remain unaffected by natural skin curvature; thus, this system is particularly valuable for applications in smart skin and biomedical contexts. Furthermore, due to its ultrathin and flexible nature, the GMR system could adhere to any flat surface, providing potential applications in diverse fields, including robotics and electronic power transmission.”The long-term stability of the GMR device was evaluated using repetitive loading experiments. Results revealed that even after 500 loading cycles (0° to 60° bending angles), the GMR ratio remained constant at 2.46%, highlighting that the GMR device remained stable despite repeated bending. Finally, the application of the GMR device as a magnetic skin capable of providing users with a sixth ‘magnetic perception’ sense was successfully evaluated.
“…it can be used on the human body for multisite pressure, particularly in patients at risk for pressure injuries, or applied to robots to provide high-resolution pressure sensing capabilities and human-like functionality.”
Conclusions
The current study describes a revolutionary manufacturing process for GMR devices using a novel electrochemical delamination fabrication process. This innovative approach not only enhances efficiency but also opens new possibilities for large-scale manufacturing. Findings highlight the development of the first flexible GMR sensor array with a spin-valve structure and enhanced sensitivity to small magnetic fields. Notably, the array demonstrated long-term stability despite repeated (500) bending cycles, highlighting its potential applications in ‘smart skin’ and high-resolution pressure sensing. This work represents a significant first step in achieving the goal of advanced integrated electronic skins with enhanced functionality and long service life.Disclaimer: This story is auto-aggregated by a computer program and has not been created or edited by menshealthfits.
Publisher: Source link